W06 Case Study Reading: Managing Projects at a Logistics Company
Instructions
Prepare for your team meeting and your individual analysis by thoughtfully reading the following case study.
Submission
After completing the reading, return to Canvas to submit a quiz about the basic case study facts.
Then, in separate assignments, you will discuss this case study with your team and complete your analysis of it.
Case Study: Managing Projects at a Logistics Company
The specific characters, companies, and projects of this case study are fictional, but they are based on actual circumstances that occurred at a logistics company.
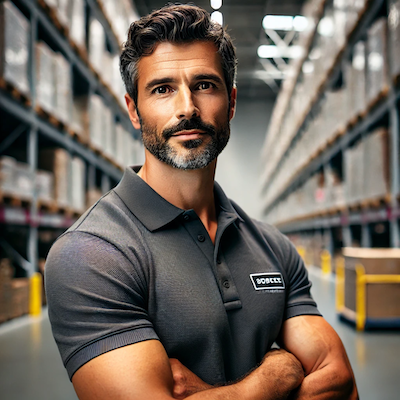
Frank Romano
Frank Romano sat in his car eating his lunch. He looked out across the parking lot at the loading dock where the large trailers were jutting out of the warehouse portals. Arrivals and departures from the loading dock were regular—the warehouse in Hebron, Kentucky was one of their busiest and that was good news. That meant that business was booming. With most of the population of the eastern United States accessible by ground transportation within 1-2 days of the Hebron location, it was easy to get goods delivered within the timeframe most American consumers have come to expect.
Frank found it very relaxing to watch the comings and goings while he ate in peace in his car. As the technical manager for the warehouse, he had to make himself scarce at lunchtime otherwise he wouldn't get any peace. Today in particular, he needed to clear his head—he had an after-action review report for the leadership team at his company to prepare, and it was not going to be easy. He had been thinking about it all day but hadn't written anything yet.
After-action review reports were reserved for those instances when expectations were not met, or things had gone terribly wrong. The report was intended to include a root-cause analysis and a recommendation of changes to policy or procedure going forward. In this instance there sure was a lot to write about—but where should he start?
Frank worked for Western Innovative Logistics Solutions, Inc. or WILS. WILS owned a series of warehouses in the greater Cincinnati area, including a large facility in Hebron, Kentucky just across the Ohio River. WILS serviced a wide variety of e-commerce companies who want to outsource their logistics operations. WILS handled everything from shipping packages to handling returns and generating reports about inventory levels and status. WILS used industry standard interfaces so that integrations with other companies were simple and efficient.
Frank had started at the warehouse years ago managing the outbound logistics systems. He had been hired to help set up the integrations with different systems. Much of what he did could be done with configuration, but often he had to write code to make it all work the way the business wanted. Before long, he was working with a team of people including coders, testers and configuration specialists. As warehouses had been added in the area, he and his team had been directly involved in setting up the necessary systems. With his intimate knowledge of the warehouse systems, he had been tapped to be the technical manager. Although he had little formal management training, he had managed as best he could with a combination of common sense and problem-solving skills.
Business had been great, but trouble had been brewing for some time now. Frank sighed as he remembered the first meeting he had with Daniel Russo, the general business manager for the region, to talk about the most recent concern.
"Frank we're in trouble," Daniel had said.
"What do you mean we're in trouble?" Frank had responded. "Utilization is at an all-time high. We still have room to grow in the warehouse, but we can handle as many new accounts as you can send us."
"It's not about capacity, it's about scalability." Daniel had returned. "You remember when we landed the GlobeMart account?"
"Well, yes. That was a huge win. We had to increase our operations space here in Hebron by 50% to accommodate them."
"Well, GlobeMart is concerned that we aren't reaching the west coast fast enough. Normal ground shipping to locations in California is still 3-4 days. This is a huge competitive disadvantage. They are telling us that they might need to find another provider that can service them from multiple locations. We've been talking about opening that Los Angeles location for months now, but this situation is forcing our hand. We cannot delay setting it up any longer."
Frank's mind immediately started to whirl. They had set up new locations in and around Cincinnati before, and they were familiar with the process. Here in Cincinnati, WILS had preferred vendors that helped them set up communications, electrical, computer infrastructure and all the necessary machines when a new warehouse was opened. Those vendors were local to Cincinnati, so they would have to find new ones for Los Angeles. In addition, another instance of the warehouse management system would have to be set up. They had done that before as well, but there was always a fair amount of custom coding required to handle the specific capabilities of each warehouse, and any unique equipment installed. This was doable, but complicated.
Daniel broke into Frank's thoughts with the expected question. "Well, how quickly can you get Los Angeles up and running, if I gave you the green light today?
This was the question that always came up. Frank knew that the minute he gave Daniel an estimate, he would be held to that. Frank had always been careful to get input from the technical team before communicating any estimates to managers. He'd been chastised in the past many times by communicating the wrong estimate too early.
Frank replied. "I couldn't guess right now without talking to my team. There's a lot of moving parts here as we have previously discussed, and although we've done this before, Los Angeles presents some unknowns that we haven't seen before."
"Well, GlobeMart needs this by the end of the third quarter, so they have some lead time to place inventory before the beginning of the Christmas shopping season. Talk to your team, but I want to hear that we can do this by end of September."
Frank looked at his phone. Today was June 26th—that would mean only three months to do this project. While it was true the usual setup of a warehouse around Cincinnati could be done in about three months, sometimes it was closer to four. This would be very tight.
"I understand. I'll talk to the team."
Later that afternoon, Frank gathered the team. Jimmy Bernardi was his most senior level programmer and was in attendance along with the rest of the team. Frank started the meeting and Jimmy jumped in immediately.
"It's about time we got started on the Los Angeles warehouse. We've been talking about it for months and we've done a lot of research on this one. I agree with Daniel that it's time to start implementing. This will be very exciting. I'm sure you'll fly us all out for a trip to the California beaches when we're done, right?"
Frank smiled, "Well, let's not get ahead of ourselves just yet. Has the team already scoped out this project? Do you know how much time you all will need?"
Jimmy said, "We created a backlog of probable tasks for the Los Angeles installation a while ago. We just went through the backlog again and estimated the tasks, but some of them are just high level and need to be decomposed a bit more. Looks like best case, we're looking at eight sprints."
Frank's stomach fell. Sprints were two weeks each which meant the current estimate was four months.
"Daniel told me that GlobeMart wants to use the Los Angeles warehouse for the holiday buying season. We need to have this done by the end of September. Do you think we can make that happen?"
Around the room concerned looks flashed across the faces of all the team members. No one dared to speak. Finally, Jimmy spoke again. "Our estimates are our best guess, and there might be some room for tighter estimation. Honestly, though, I just don't know how easy it will be to fit this into three months. Four months was our best-case scenario, which is more like late October. It wouldn't surprise me to see this continue into November a bit."
Heads nodded in agreement. Looking around it was clear that late September seemed out of reach for the team. Frank said, "I see. Let me take this back to Daniel and see what he thinks."
Frank was now between a rock and a hard place. He was already sure he knew what Daniel would say, but he had to make the call anyway. Frank called Daniel who picked up the phone quickly. "So, can they do it in Q3? We really need this."
Frank paused a moment, "The team estimated four months for the project, but some of the estimates are uncertain. It's possible we could squeeze some more time out of the estimate if we look carefully."
Daniel replied, "That's not an answer. Can they do it in three months or not? GlobeMart will not be happy if we cannot deliver this to them. We stand a very good chance of losing that business—and you know that might mean reductions for your team without that revenue. I've heard through my sources at GlobeMart that they are already in discussions with other logistics vendors if we cannot meet their needs."
Frank was stunned. He didn't realize so much would be riding on the ability of the team to do this in three months. "Daniel—I'll be sure to tell the team to try their best to make that three-month mark."
"Very good. Keep me up to date on how things are going." Daniel ended the call, and Frank was left to consider what his options really were.
Frank reached out to Jimmy for a copy of the planning estimates. Maybe he could find a way to squeeze some time out of the schedule. After looking over the estimates, Frank found a few items he thought were overestimated. He also saw a couple of items he thought could be put off until after the go-live date, like a proposed WMS software upgrade. He thought that some efficiency might be gained by doing a few other things in parallel. Using his favorite spreadsheet, Frank put together a plausible schedule for doing the work in three months. He quickly dashed off an e-mail to the team with his proposal attached.
A few minutes later, Jimmy stopped by Frank's desk. "I don't understand your e-mail. I thought we decided on four months. Isn't that what we estimated?"
Frank replied, "I had to tell Daniel that we'd do our best to make it in three months. The business is anxious not to lose the GlobeMart account and we're at risk if we cannot make it by the end of September. I think if we follow the plan as I've outlined, we can make it."
Jimmy grumbled. "You know there is no way we're going to make this."
Frank shrugged and Jimmy turned and left the area.
Work began on the project in earnest. All other projects were suspended to focus solely on the Los Angeles warehouse setup. Frank was initially hopeful, but the problems started almost as soon as the project got going.
First, Sylvia, the web frontend developer abruptly left the team. Her mother who lived in Iowa had been unwell and Sylvia had hinted several times that she might have to move to Iowa to care for her. Only two weeks into the project Sylvia dropped her news on the team. She had found another job in Iowa close to where her mother lived and was moving. She could not be persuaded to stay on and help, even in a remote capacity.
Frank and Jimmy discussed the situation. Jimmy suggested to him that the backend developers had plenty to do before the user interface was needed. Jimmy was hopeful that this lead time would allow some time to find a suitable replacement before it was critical.
Frank agreed and the team pressed forward. But the team struggled to find a suitable replacement for Sylvia. The market for developers was very competitive and working at a logistics company was unglamorous. No one wanted to join the team at WILS.
More weeks went by, and the backend team had done almost all they could do without help on the frontend. Towards the end of August, Frank went to Daniel to share the news.
"We're in big trouble here without a frontend developer. We are almost at the end of what we can do on the backend. I'm not sure how we make that date."
Daniel was unmoved. "You should have had someone in place immediately to backfill Sylvia. Did you not think to hire a temp worker?"
Frank replied, "We looked into temp workers but couldn't find anyone who knew our frontend framework. Some that claimed to know it didn't pass the technical interview when we met with them."
"What about Julio in our Cincinnati office? Does he know the frontend?"
"I'm sure he does, but isn't he busy on the returns team? I think the returns team operates out of that office."
"I'm sure they can spare him for a few weeks. I'll call over there and get him on your team ASAP."
Frank was grateful for the possible help, but also concerned. The project was already running late, and Julio would have to get up to speed on all aspects of the warehouse management system, not just the returns portion. Cross training Julio would take away precious time from other developers who were already working hard.
After reaching out to the returns team, they agreed to give Julio to Frank at the beginning of the next sprint which was still 10 days away. The returns team was very unhappy, because they were also working on a project with a deadline at the end of Q3. Daniel decided to move Julio anyway.
Julio started at the beginning of September, but the work moved forward very slowly. Julio tried to onboard as quickly as possible, but he wasn't sure where the code and components he needed were found. Documentation was spotty, and Julio was constantly reaching out to Frank or Jimmy with implementation questions.
Meanwhile, other problems had arisen which were unexpected. The electrician who was contracted to install the power equipment in Los Angeles ran into a problem with his supplier. The electrician started the power installation but had to stop partway through because of missing parts. The delay lasted an entire week, but Frank's team had been planning on computers and equipment being up and available for testing to meet the tight timeline. The testers worked on improving their test cases, but no meaningful testing work could be completed during this time. Frank called the electrician in Los Angeles every day for updates, but nothing could be done.
With only a few days to go, the equipment was finally installed, and the computers were up and running. However, the warehouse management software that ran on the computers had just released a new version, and some of the modules had "breaking changes". That means that the existing interface would not work with the newest version of the software. Additional changes would have to be made. According to Frank's original timeline, the older software release should have been already installed by now, and the upgrade could have been scheduled for later. Frank was counting on handling those breaking changes after the go-live date.
Frank had previously spoken to the account representative from the warehouse software management and he had been assured that the older version would be available to install even if things ran late. Despite this, the technician who showed up to do the installation was not able to do it. Angry phone calls went back and forth between Frank and the vendor, but installing the older version was a technical impossibility. This was the final catastrophe. There was no feasible path to completing the project on time.
Daniel scheduled a meeting with Frank, the development team and Daniel's boss Mark Lunden, the Chief Operations Officer. Daniel demanded an accounting of why the promised project was not going to be delivered. GlobeMart had been promised an operational warehouse in California by Sep. 30th and now Daniel had to communicate that this wouldn't happen. The meeting was to be held first thing in the morning on Friday.
Frank finished his lunch and returned to his desk. The cursor flashed ominously on the still blank document. The after-action report needed his full attention now and he had to organize his thoughts. There were so many questions with only difficult answers. What should he tell the board? How did things go so horribly wrong? What could he, or any of them, have done differently? What changes will he need to make to prevent this from happening again?
He needed to come up with a plan or he was sure the leadership team would come up with one of their own that may or may not include him.
Footnotes
- Warehouse management systems (WMS) help manage the complexity of shipping operations. Many WMS systems use industry standards but must still be highly customizable to meet the needs of individual businesses. For more information about warehouse management systems see https://www.sap.com/products/scm/extended-warehouse-management/what-is-a-wms.html. Back to content ↩
- The following shows the ground shipment times from Hebron, KY.
Map of ground shipment transit times from Hebron, KY. Image generated from: https://www.ups.com/maps/ . Back to content ↩
-
In American commerce, it's typical for organizations to make short term plans in 3-month increments called “quarters”. Publicly traded companies who receive funding from the sale of stock must report their financial situation to investors after the conclusion of each quarter. If a company doesn't perform well in a given quarter, the price of their stock can be impacted significantly. The abbreviations Q1, Q2, Q3 and Q4 are typically used to refer to the 3-month periods ending Mar 31, Jun 30, Sep 30 and Dec 31 respectively.
See https://www.investopedia.com/terms/e/earningsreport.asp for more details. Back to content ↩
Other Links:
- Return to: Week Overview | Course Home